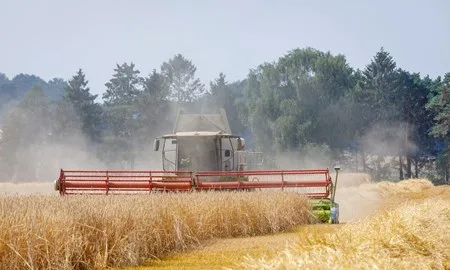
Check out our practical guide on calculating cost of production on arable farms - part of our series of posts on costs of production.
Author
| 21st September 2018How to calculate unit cost of production on arable farms
If you haven’t already read 5 reasons to calculate costs of production, that’s a good place to start; in this piece, we provide practical guidance around the process involved.
At a high level, the calculation for production cost per tonne is relatively simple:
Add together all variable and fixed costs (£/ha)
Then divide the total by the average yield for £/t
Including all costs provides the most accurate measure of overall profitability and is very different from gross margin calculations, which exclude fixed costs, and are typically used for simple benchmarking or comparisons.
While the basic CoP calculation is simple enough, collating information and allocating the correct proportion of costs to the enterprises being benchmarked, is complex, especially when done for the first time and where resources are shared across enterprises.
Cost allocation has a big impact on 'cost per tonne' and will be covered in more detail later in this series.
What to include in total costs
The variable and fixed costs that make up total cost of production are broken down as follows:
Variable costs
Generally refers to costs that can be “readily allocated” to an enterprise (e.g. a wheat crop) and vary in direct proportion to its scale, even small changes.
Includes:
Seed - purchased seed bought and/or used in the benchmarked crop year, plus the cost of any home-saved seed, including cleaning, dressing, seed treatment and royalties
Fertiliser - includes lime, artificial fertiliser and any organic manures/slurry or digestate
Sprays - herbicides, fungicides, PGRs, insecticides, slug pellets
Miscellaneous - e.g. agronomy charges, drying costs, soil tests, levies, weighbridge charges, trace elements.
Fixed costs
These costs cannot be readily allocated to a specific enterprise and do not vary with small changes in its scale.
Includes:
Labour - regular, casual (including contract labour) and allocation for any unpaid family members - only relevant to any manual, non-management work done
Power & machinery, including:
Depreciation (i.e. how much an item drops in value over its expected useful life). Calculated by: purchase price - expected value at time of replacement, divided by number of years owned
Cost of spares, repairs, fuel, other running costs
Contractor charges
Insurance and service agreements
Share of general farm vehicle costs (e.g. farm pickup).
Finance payments - interest on loans, overdrafts, hire purchase agreements, plus bank charges & fees (include the capital element of leasing charges within depreciation)
Overheads - farm maintenance (e.g. building repairs, hedge cutting, ditching), water & electricity/gas/oil (excludes costs for farmhouse or diversification projects)
Property depreciation (applies to more recent buildings/structures, plus drainage investments and mole ploughing)
Miscellaneous overheads, e.g. property insurance, professional fees (e.g. accountant, consultant), subscriptions (including crop assurance schemes), secretarial admin, etc.
Rent (or imputed rental equivalent for owner-occupiers) - varies widely depending on tenure and borrowing requirements.
Once all costs have been added together (total £), divide this by the relevant cropped area (ha) to arrive at a total cost (£/ha) and then divide this by the average yield for total costs on a £/t basis.
Use average yields
Given the impact yield variations have on cost per tonne, it is generally better to use average yields over several years - at least three, ideally five or more.
Any changes to business structure based on CoP analysis should equally be based on several years’ worth of data, and not a knee-jerk reaction to one year in isolation.
CoP data can be combined with yield maps to map “profitable tonnage” [link to section on using CoP data when live]
Start simple
Collating financial information and breaking it down for detailed analysis of specific costs can be daunting and requires accurate information to start with.
To make it easier, start by approaching costs on a broad basis and then go into more detail once recording and benchmarking processes have been established.
For example, start by measuring costs for “arable” or “cereals” enterprises as one, then, if it is possible to split out costs in more detail, consider breaking costs down into specific crop types (e.g. winter/milling/feed wheat/ malting barley, etc).
Recording a variety of information throughout the season helps to measure and allocate costs accurately. We’ll be providing more detail on this later in this series.
Where to find the information
Farm financial accounts contain much, but not necessarily all, of the information required. For example, they often don’t include a figure for unpaid family labour, which will have to be estimated.
Also remember that financial records may have a different year-end to the crop season, which typically runs from September/October to August/September.
Farm management and crop recording systems, such as Farmplan’s Gatekeeper, Muddy Boots Greenlight Grower Management, and others (e.g. Sum-IT, Landmark Systems), also contain useful data, although often focus on variable costs, agronomic inputs and physical measures of crop performance.
Other specific records (in hard copy or digital format) kept up-to-date throughout the season can also be invaluable when collating and allocating costs. More on this in our ‘Measurement’ section.
Systems to measure Cost of Production
Many farmers have their own preferred ways of analysing and calculating production costs, based on existing records and IT software, but there are also systems available to help.
The AHDB Farmbench online cost analysis and comparison tool, for example, allows farmers to input their own financial and physical data to calculate total production costs at an enterprise or multi-enterprise level. Many farm business consultants also offer cost analysis and benchmarking services.
Many thanks to Sebastian Graff-Baker at Andersons and other industry contacts for their help compiling this information.
We’ve got lots more advice on costs of production on the way. Follow us on Twitter @Bayer4CropsUK to keep up with the latest from our blog.