Published on 4th March 2024
Weed Management
Mechanical weeding options on the rise
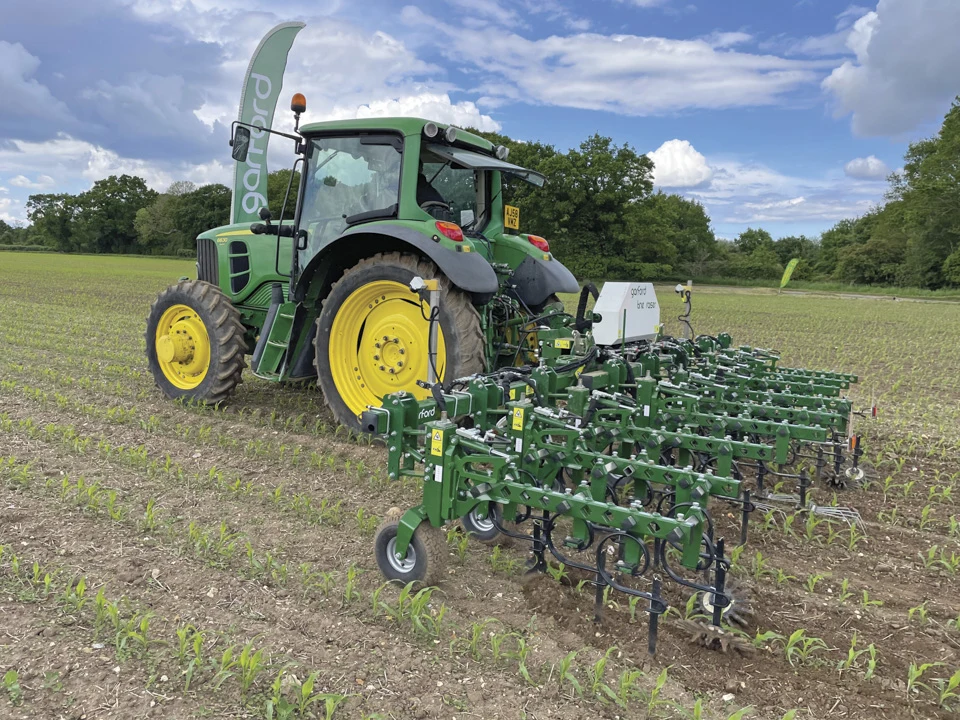
A drive towards more sustainable farming techniques and a reduced chemical armoury is sharpening the focus on mechanical weed control methods.
Such is the uptick in demand for mechanical weeding tools, scores of mainstream arable machinery makers have been busily snapping-up makers of specialist weeding equipment.
Lemken, Väderstad and Amazone are notable examples, recently purchasing respective brands Steketee, Thyregod and Schmotzer. But there are plenty of other firms that have either begun importing, or building, their own versions of these implements.
Firms formerly routed in the specialist crop sectors have also rallied to adapt their product ranges to make them suitable for combinable crops.
With the help of agronomist, Will Smith, and a few key manufacturers, we look at the range of equipment on offer and provide some tips for how it can be best used.
Inter-row hoes
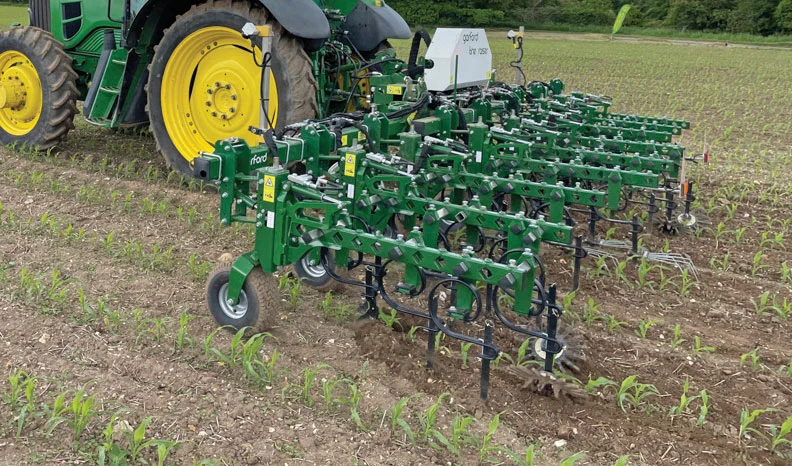
Garford Robocrop inter-row hoe
Using a series of evenly spaced tines, shares or blades, inter-row hoes carefully uproot weeds that have established in the unplanted spaces between crop rows.
Basic versions are fixed implements that rely on guidance or a sharp-witted operator to keep them in line. But a more precise option is to opt for a camera guided version. These detect where the crop is growing and use a side-shifting hydraulic mechanism to make sure the weeding elements stay in precisely the right place.
In trials carried out for his PhD on the effects of inter-row hoeing on black grass populations in wheat, Mr Smith found the process gave between 15% and 30% additional control on top of a typical herbicide programme.
“This makes it a valuable process, particularly in years where chemical controls are less effective,” he says.
“Back-to-back spring cropping has become popular for those struggling to control the weed, but the effectiveness of using a hoe may allow growers to re-introduce an extra winter wheat.”
Those in the market for an inter-row hoe have plenty of brands to choose from, many of which use a similar setup. Typically, they are built in a modular format, meaning they can be configured to work in crops planted at most row widths. This means one machine can easily be adjusted to work between maize rows at 75 cm spacings, sugar beet at 50 cm, or cereals at 25 cm.
Wider band-sown cereal crops lend themselves most readily to the technique, but some models are capable of working between conventional 12.5 cm spaced crops.
Although, there is a greater risk of crop damage when working this narrow, and a far smaller proportion of the field is weeded.
Garford is an established name in the mechanical weeding game and its Robocrop inter-row hoe works with a separate hydraulic side-shifting frame, guided by a camera system from UK firm Tillet and Hague.
Prices start at about £40,000 for a 4 m version with 16 rows set at 250 mm, and a 12 m model with 12 rows at 750 mm is about £65,000.
The best timings for using these machines vary considerably according to the season, so users need to assess the conditions rather than work off a calendar.
“You need some soil moisture for the hoeing implements to do their job, but you don’t want enough for weeds to re-establish,” says Mr Smith.
He thinks the next steps for these implements will be a broader array of hoeing tools that will help them work in a wider range of conditions, allow them to get closer to the crop, and better destroy uprooted weeds.
Intra-row weeders
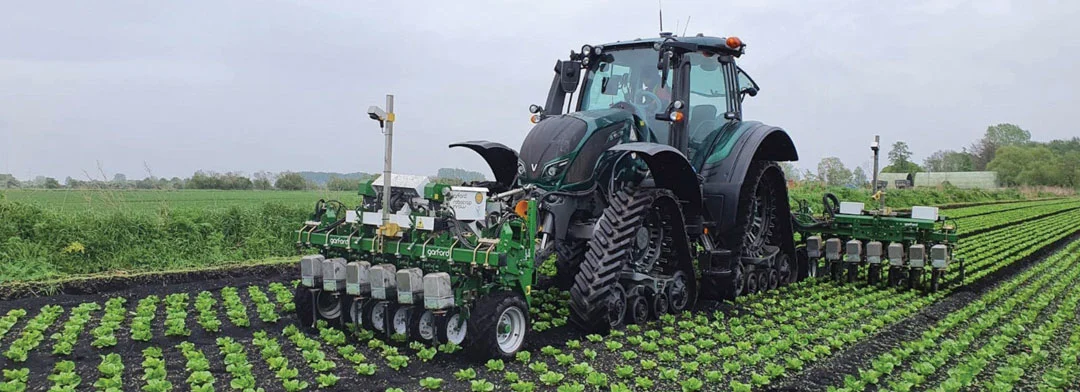
Garford Robocrop Inrow
By fishing out weeds growing between plants within the row, intra-row weeders, such as the Garford Robocrop Inrow, and Lemken IC, have the potential for a higher level of control than their inter-row cousins.
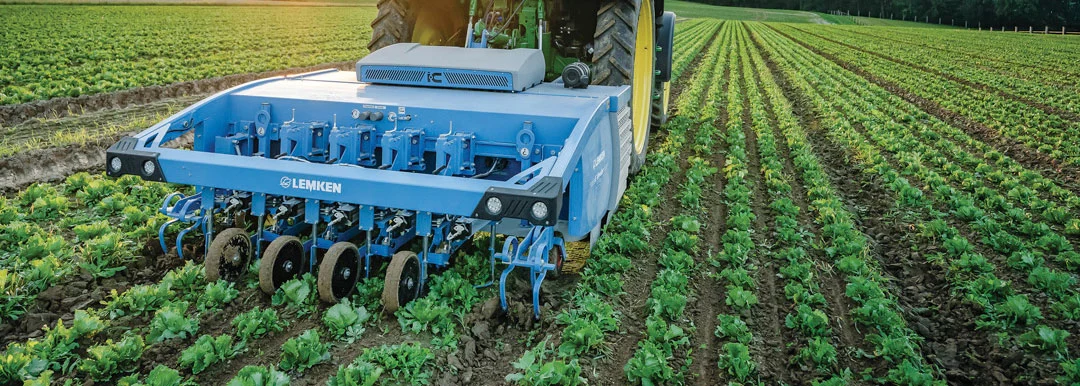
Lemken IC
However, these high-tech machines are not really suitable for cereal crops, as plants are too tightly spaced along the row for their camera-guided tines to pass between.
They are primarily designed for veg and salad growers, where the high costs can be better justified, but there is potential for them to be used on precision-planted crops, such as sugar beet or maize.
Even if they were suitable for cereals, the additional benefits would be minimal as weeds tend to be outcompeted in the crop rows, notes Mr Smith.
However, he does see potential for simpler finger weeders that get closer into crop roots and help flick out some of the weeds growing between plants.
In-crop weeders
A simpler approach to mechanical crop weeding is to use a tool that works the entire field.
These are generally a simpler and faster option than inter-row hoes as they do not require a camera guidance system, nor do they have to be used with GPS.
They work on the principal that the crop will be better rooted than the weed, so growers need to time their use carefully. Go too early and plants could get damaged, but too late and the weeds will be too well established and the soil could be too hard.
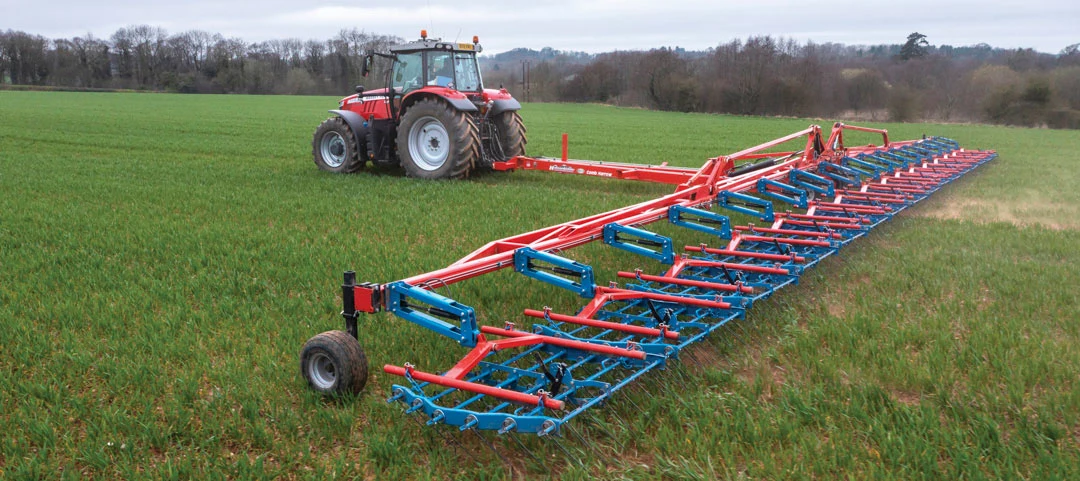
Hatzenbichler Comb Harrow
In the UK, there is a very short window for these tools to be useful. “In the autumn, they’re only really suitable for early September drillers, which is the last thing you want to be doing if you’ve got a grass-weed problem.
“But, they could have more of a role for weeding spring crops.” says Mr Smith.
Comb weeders, such as the Hatzenbichler Comb Harrow imported by Opico, are one example, featuring several rows of lightweight tine harrows that flick poorly-rooted weeds out of the ground. This particular machine is available in working widths from 1.5 m, up to a huge, tramline-friendly 24 m.
Another option is a rotary implement, such as the Pöttinger Rotocare. This has a series of spiked wheels with spoon tips that flick out weeds without damaging the crop.
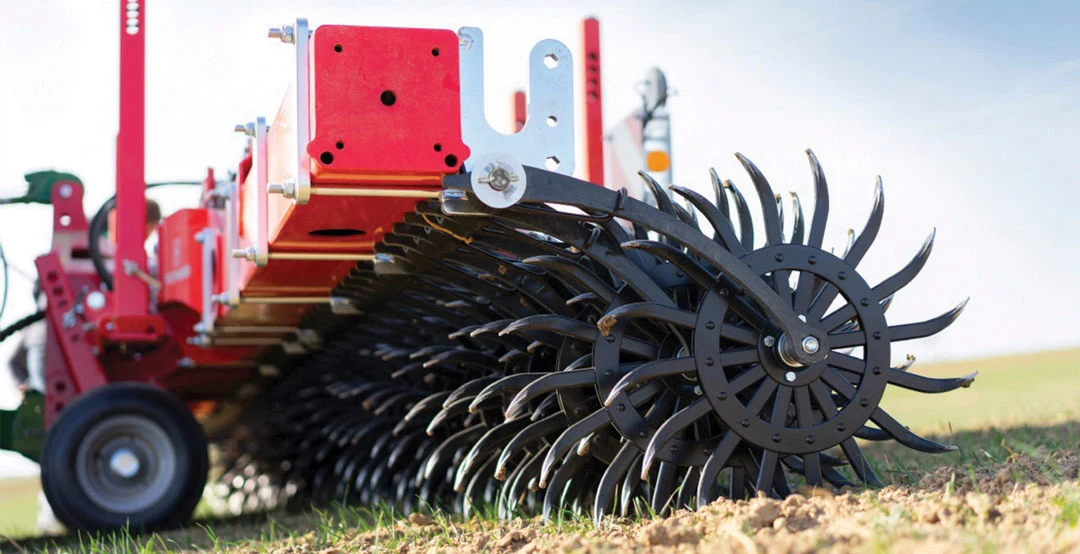
Pöttinger Rotocare
Pöttinger recommends using it in late autumn or early spring, depending on conditions, and says some soil moisture is desirable for helping it work effectively. It can also be used as a light stubble cultivator, soil crust breaker and grassland aerator. The popular 12.4 m version has a retail price of £59,135.
Weed surfers
Their action of decapitating weeds before they have shed seed allows weed surfing tools to reduce the seed burden for following seasons.
Simple versions, such as the Lyckegard Combcut and Bionalan, cut seed heads off weeds standing above the crop, before dropping them to the ground. This helps keep costs down, but timings have to be spot-on to ensure seed has not reached a viable stage.
A more sophisticated setup is the Zurn Top Cut Collect, which collects harvested seed so it can be removed from the field and disposed of.
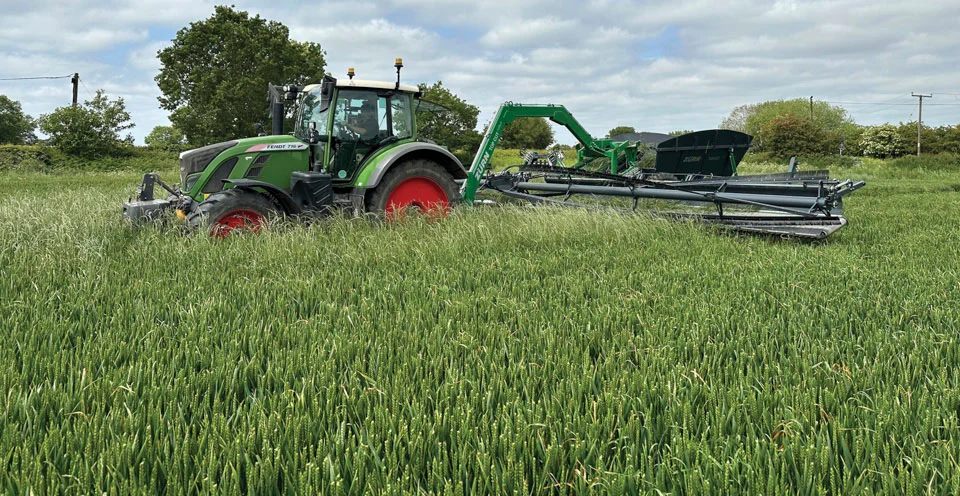
Zurn Top Cut Collect
NIAB trials found it was up to 90% efficient at removing black-grass heads when set close to the top of the crop and used at the optimum timing. Generally, this is when weeds are mature, but have not yet shed seed, maximising the number of plants above the crop canopy.
“If used correctly, it’s another useful tool for reducing weed pressure and complements tools such as inter-row weeders,” says Mr Smith.
The Top Cut Collect is a complex and expensive machine, with the 12 m version coming in at £113,500. For those without the workload to justify it, there is a roving contractor in the UK running two of these machines.
Harvest weed seed control
A final opportunity to manage weed pressures before the end of the season is to tackle any seeds coming out of the back of the combine.
The simpler method of doing this is to concentrate chaff into a narrow band, so that problem species are easier to manage. The EMAR Chaff Deck is one option, bolting in place of the chaff spreader to concentrate material in wheel marks rather than spreading it across the entire field.
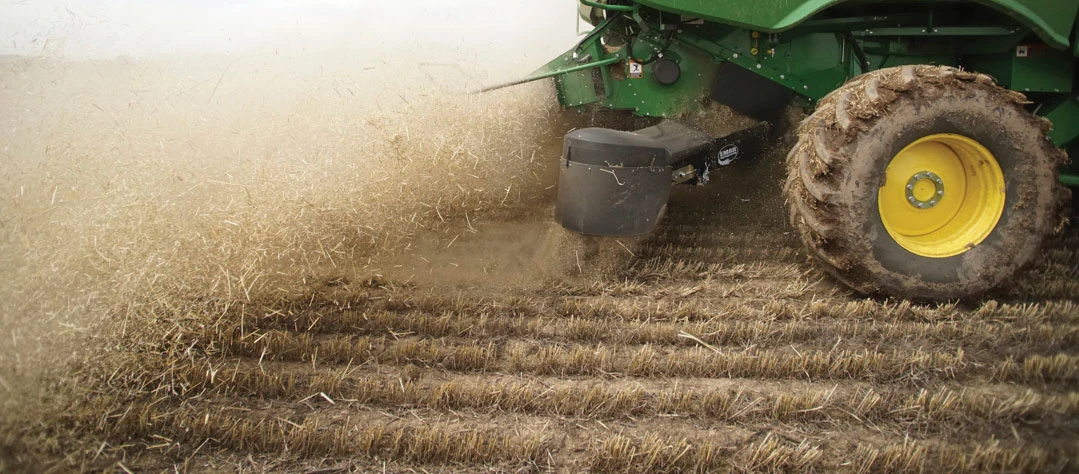
The EMAR Chaff Deck
Tools like this are more practical for the UK than bulky carts that collect all chaff and remove it from the field.
Destruction of weed seeds using a device fitted on the back of the combine is also possible. Examples include the Harrington Seed Destructor, Redekop Seed Control Unit and the Seed Terminator.
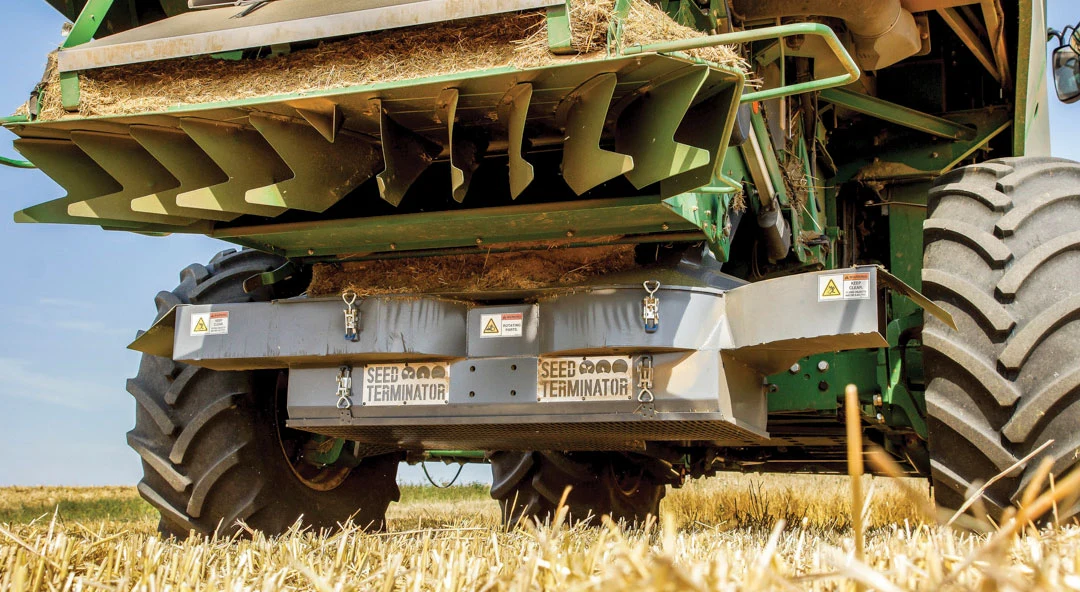
Redekop Seed Terminator
Each has a slightly different design, but they all use a precise milling machine that crushes the tiny seeds so that they are no longer able to grow. Trials have, and are being carried out in the UK, on both the chaff deck and seed mills, which have given some encouraging results.
“It’s just worth bearing in mind that a good portion of weed seeds are shed before harvest, particularly black grass, so these tools ideally need to be used in conjunction with other control measures to make a significant difference,” says Mr Smith